Process
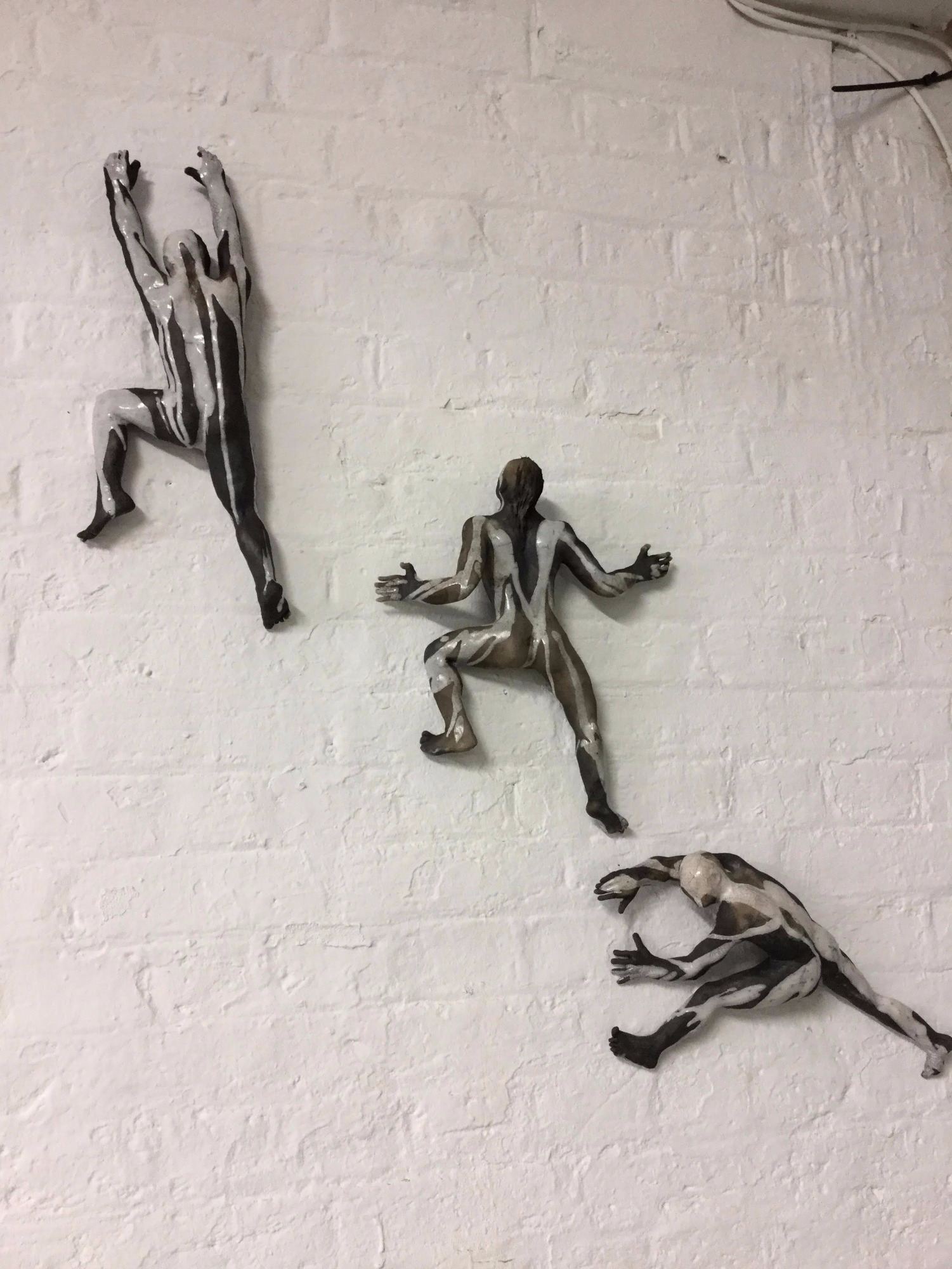
The Raku Process
All work is biscuit fired in an indoor electric kiln. A high alkaline frit glaze is then applied before the work is then taken outside to be raku-fired in a gas kiln..
Work is placed in the gasfired raku kiln
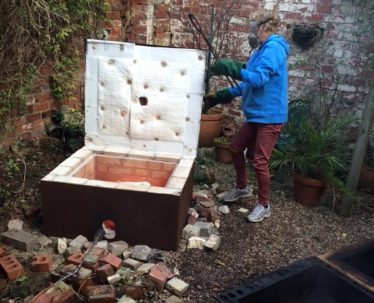
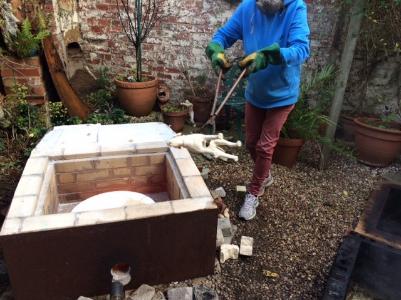
When the glaze reaches about 900 degrees the lid is opened and the work is swiftly removed using tongs.
Next the work is placed in a smoke pit...
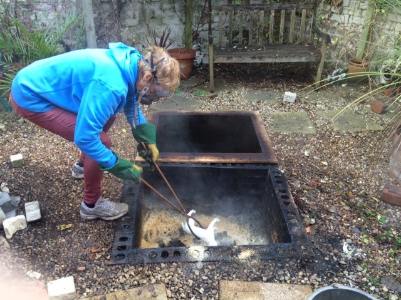
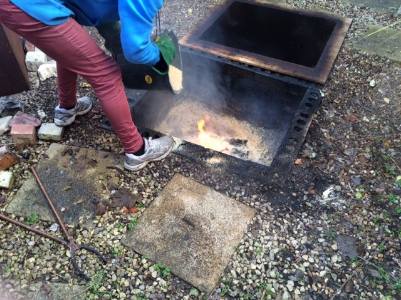
...covered with sawdust, and the lid replaced to stop the flow of oxygen.
After around 20 minutes the now-blackened sculpture is removed. The glaze has crazed and the gaps filled with carbon to give the black and white crackled effect.
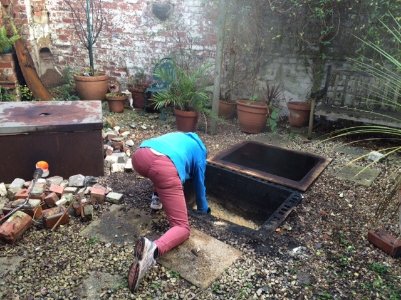
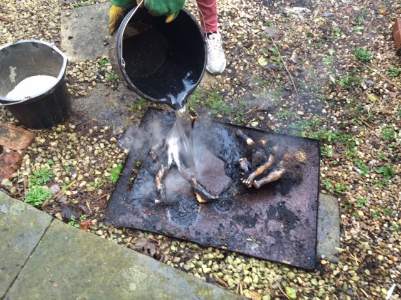
Water is poured over the sculpture to extinguish any flames and cool the work.
Back in the studio, the work is cleaned up using fine brushes and wire wool.
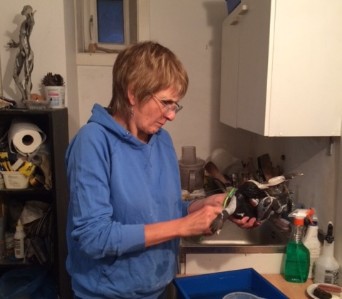